[ad_1]
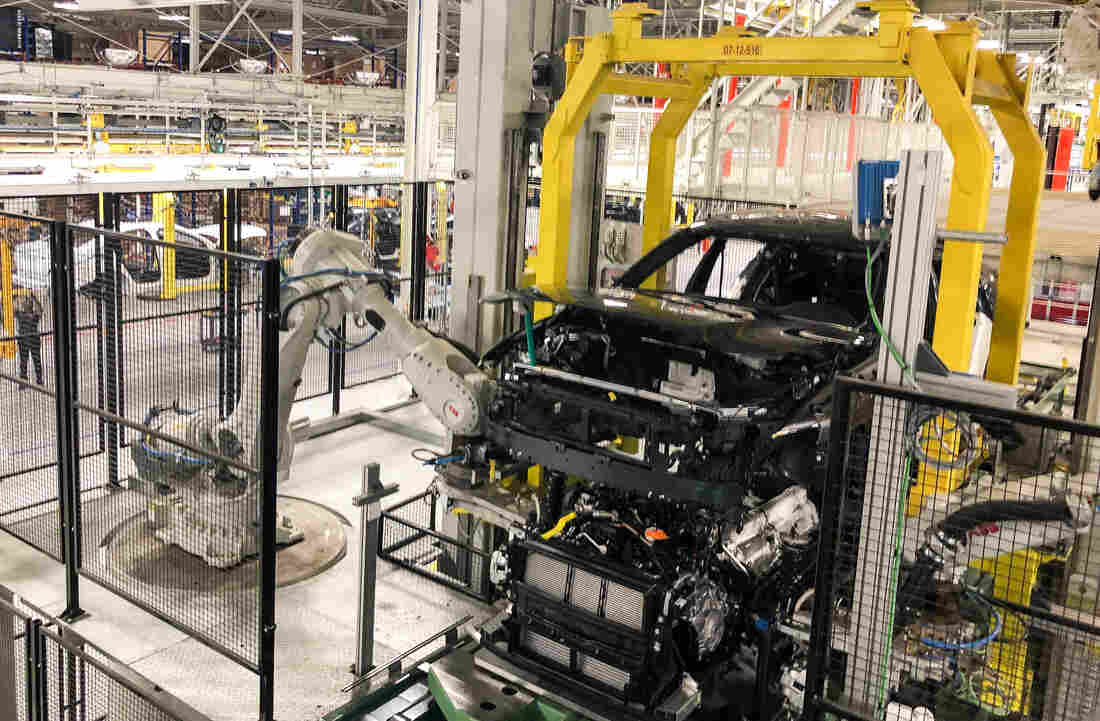
A robotic arm is working on the production line at the Volvo plant in Ridgeville, S.C. However, other key tasks, including most of the final assembly, are still left to people.
Camila Domonoske / NPR
hide legend
activate the legend
Camila Domonoske / NPR
A robotic arm is working on the production line at the Volvo plant in Ridgeville, S.C. However, other key tasks, including most of the final assembly, are still left to people.
Camila Domonoske / NPR
Robots have revolutionized car manufacturing by making factories safer and products more reliable – and reducing the number of people involved in the process. But enter a modern car factory and you will quickly realize that robots have barely replaced human contact – at least not in some areas.
The Ridgeville, South Carolina auto plant, which opened last year, provides a lesson to remember. The factory produces the S60, a luxury sedan, for the US market as well as for export.
The beginning of the production chain is highly automated. in the first of three large buildings, robots are 300 to 200 in number of human workers. But the end of the process is dominated by people.

Let's start with the robots. Behind a safety barrier, half a dozen robot arms move in a coordinated fashion when they spot weld a car body, simmering gently. The lights in this section of the huge building are dimmed because the robots do not need a lot of light to complete their work.
Robots are indisputably better than humans for some tasks. They are accurate and consistent, and they excel at repeating an identical motion over and over again.
Jeff Moore, vice president of manufacturing at Volvo in America, says that when deciding what tasks to assign to a robot, the company starts focusing on monotonous and physically demanding work, especially on safety issues.
"With all the heat, sparks, high currents and similar elements to welding, it's natural to look for where you can automate more intensely," he says.

But in other parts of the line, "human contact has a lot of benefits," says Moore.
Or as Tesla CEO Elon Musk Put the last year, "humans are underestimated".
He admitted that Tesla had miscalculated by turning to heavy automation on his assembly line in Fremont, California. Once the production problems arose, the electric car manufacturer reversed the trend and started giving people tasks.
So where exactly do humans still beat robots? Follow the body of the car along the Volvo assembly line and the lights come on when humans are securing the hood, trunk, fenders and bumpers.
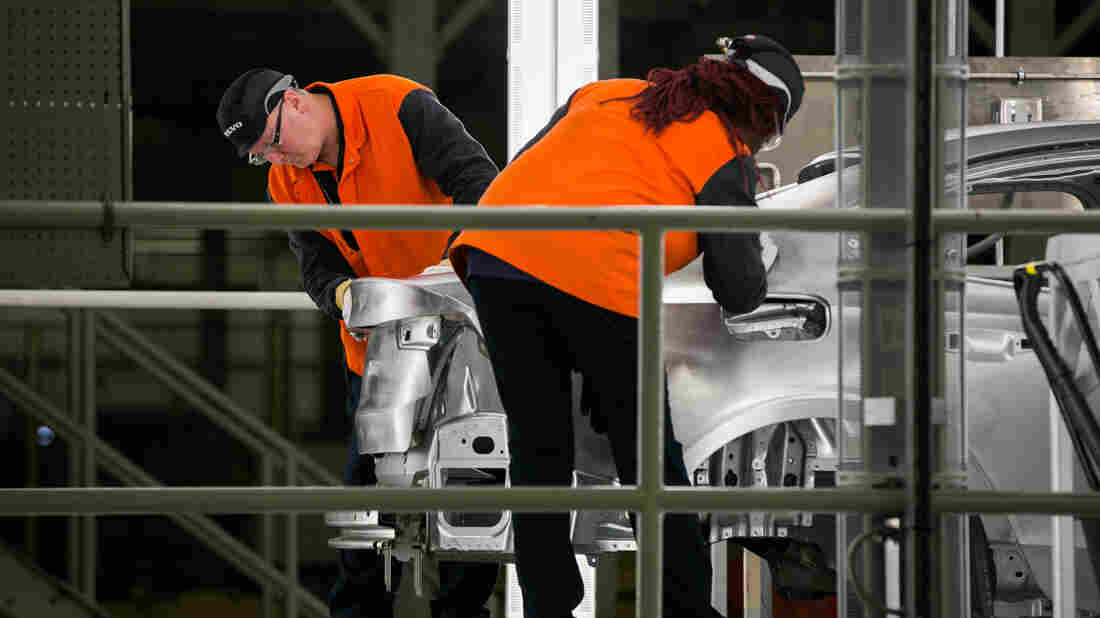
Workers inspect the body of a Volvo S60 sedan on June 20, 2018. Robotic sensors examine welds, but human hands and eyes gauge the feel and feel of the metal.
Logan Cyrus / Bloomberg via Getty Images
hide legend
activate the legend
Logan Cyrus / Bloomberg via Getty Images
Workers inspect the body of a Volvo S60 sedan on June 20, 2018. Robotic sensors examine welds, but human hands and eyes gauge the feel and feel of the metal.
Logan Cyrus / Bloomberg via Getty Images
Then comes the quality control. Robots equipped with sensors test the welding spots and people run their hands over the surface of the metal body, looking for imperfections. The literal human contact still can not be beaten here.
The body of the car crosses an overhead bridge to another building, where it is painted – another task for which the robots excel. Then he goes to a third building for final assembly, where thousands of pieces from around the world come together to form the finished car. Here again, humans reign.
People are better able than robots to manipulate complex shapes and assemble them – exactly the skills required to attach parts to engines, for example.
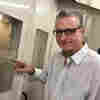
These workers also handle different types of engines – gasoline or hybrid, all-wheel drive or front-wheel drive, with or without turbo and, in the future, even fully electric engines. Humans can easily move from one task to another and even pick new ones on the fly; not so much robots.
While Tremaine Smalls attaches drive shafts to the engines, a radio reporter interfering occasionally, he avoids the complications of working with different types of engines.
"It's a bit of the same process, just different drive shafts," he explains, showing how he checks part numbers on a piece of paper to confirm that each motor is properly configured.

The Volvo plant depends on people who want to attach drive shafts and other parts to the final production line. Workers check the part numbers against the paper prints attached to each motor.
Gary Coleman / Courtesy of Volvo Cars America
hide legend
activate the legend
Gary Coleman / Courtesy of Volvo Cars America
The Volvo plant depends on people who want to attach drive shafts and other parts to the final production line. Workers check the part numbers against the paper prints attached to each motor.
Gary Coleman / Courtesy of Volvo Cars America
Jason Dodgins, working on the same line, was formerly a team leader for a bearing manufacturer. There, he says, his job was to operate a computer controlled machine.
"The machine has done a lot of work," he says. "You were basically doing the inspection." Working on this automotive assembly line, on the other hand, "requires a lot more manual work," he says.
As the engine moves along the line, humans and machines share the work. Kayla James, just two weeks after taking office, uses a mechanical lift to install an exhaust system. it removes the physical tension of the task. Later, a big machine simultaneously installs dozens of bolts – but between each cacophonic volley, Brandon Marshall loads the various bolts in place.

Humans master robots in these tasks even when things are going well, but they have a particular advantage in case of a problem.
In modern automobile plants – inspired by Toyota's revolutionary production philosophy – workers are encouraged to stop the chain whenever there is a problem, whether it is big or small. (In factories like this Volvo factory, workers pull a rope and listen to music – a different song for each location indicates that a problem has occurred.)
Robots can also identify some errors, but humans have a distinct advantage in terms of the resolution these problems.
Consider Volvo radiators. At a key point in the line, the body of the car – waiting in a raised conveyor – goes down on top of the engine, transmission, axles and everything that moves the car. They meet at the "point of marriage".

"If this radiator is not sufficiently repulsed, it will break with the body," says Trey Yonce, who helped set up the marital dividing line.
The initial production process provided elastics to hold the radiator in place at this key moment, but a laser sensor frequently detected that the radiator was not exactly in the right place. Machines can signal the problem to be solved.
But humans, unlike robots, are annoyed by repeated problems.
"They just got tired of it, and a guy came up with an idea and it worked," says Yonce. It indicates a small piece of yellow plastic that retains the radiator more effectively – an improvement in the process.

Mr. Moore, Volvo's vice president, said the company had already filed several patents based on ideas from workers at the new plant.
Humans have assets, compared to robots, in all kinds of workplaces – not just car factories.
And in general, people and robots work better together, robots handling dangerous, monotonous work and precision work, while people manage touch work, change tasks, make decisions – and come up with creative ideas for improve things.
There is a philosophy lesson here, in a way.
"People often think that manufacturing workers are a poor substitute for the robot," says Susan Helper, an economist at Case Western Reserve University. Like a machine that complains, gets tired and makes mistakes.

And historically, some factories have tried to treat their workers as robots, separating the "brain work" from the work "by hand" and pushing the workers to the assembly line to do repetitive tasks without thinking. In this configuration, a robot is an upgrade of a human worker: he does not complain and does not tire himself.
"But in practice, these things are really difficult and the assembly line manager is often discerning," says Helper. "And it turns out that when you take that person, you end up with hard-to-solve problems."
This means that the best thing robots can do for manufacturing is not to replace people, but to release them so that they can work as people.
[ad_2]
Source link