[ad_1]

Running is a useless sport. Every year, billions of shoes are made, worn until they begin to fall apart and are thrown into a landfill. It is estimated that 300 million pairs of running shoes are thrown away each year in the UK alone.
As part of a long-term plan to avoid excess waste, adidas reconfigures its plants to produce footwear that can be ground into pellets, melted and transformed into new running sneakers. Futurecraft.Loop is the first experimental shoe of this type.
At first glance, the running shoe does not look very different. It's an off-white sneaker made up of all the usual components: a foam midsole, an outsole, a knit upper, an insole, laces and a torsion bar that contribute to stability.
Loop stands out for its manufacture and redesign. The adidas engineers made the whole pair of shoes out of a material, a version of thermoplastic polyurethane (TPU). On average, other adidas sneakers consist of at least 12 different materials. "The concept is that this shoe is 100% recyclable and zero waste," says Tanya Sahanga, a materials engineer from the adidas Futurecraft team, who has already experimented with 3D printed trainers and fabricated trainers. from plastic pollution from the ocean.
"We are getting first-generation shoes," said Graham Williamson, Senior Director of Future Apparel at adidas and Loop Project Manager. "We will recycle this and use this recycled material to create components for the next shoe."
To recycle the shoes, adidas has them washed and sent to one of the factories of its industrial partner ASF. Once here, the material is ground into fine granules and then remelted in its original state, from which it can be converted into a shoe.
Crucially, the TPU can be melted once it has been used. TPUs are a type of polyurethane plastic and are known for their elastic properties, transparency, high resistance to oil and grease. This is not the first time that the company uses a variant of TPU in its shoes; In February 2013, adidas introduced its Boost foam, which is used in most of its midsoles, after working with the German chemical manufacturer BASF.
When used in a midsole, Boost is made up of 2,500 TPU elastic beads that are pressed into a mold to create an incomparable rice cake look. "The stem is made of the same material," says Sahanga about Loop. (It's an off-white color because there's no bleaching agent that gives the trainers an immaculate white appearance, she says). The problem for his team was that even though the TPU can be handled relatively easily in the midsole, it is much harder to turn it into a wire for creating a shoe upper.
The breakthrough of the project, which has lasted six years, took place in 2016 when engineers modified the plastic to transform it into a traditional thread type fabric. "TPU is available on the market, but we have developed one specifically for us and we have advanced it," says Sahanga. Previously, adidas did not have any material to create a complete shoe. Traditionally, the running shoe's upper was polyester.
"At the beginning of 2017, we could manufacture shoes and components several times, before we could only make one or two shoes at a time," says Sahanga. "We made a lot of 50."
The best running shoes you can buy in 2019
Creating a new type of thread for the top was not the only problem. The glue with which the shoes are badembled can not be easily broken during the recycling process. Workers who bademble shoes with glue should wear masks to protect themselves from fumes. To solve this problem, adidas has completely removed the glue from the shoes. Instead, he uses lasers to solder the parts of the shoe.
The technology was developed in its first speed plant in Germany. There are now two speed factories, the other is located in the United States, and robots bademble adidas trainers in less than a day. The factories allow adidas to go faster in its manufacturing operations and avoid any dependence on Asian factories, where over 90% of the 360 million trainers are manufactured each year.
Traditional plants can be ineffective for the environment. Landfills and environmental impacts are a huge problem for sports manufacturers and the fashion industry as a whole. A 2012 study by researchers at the Mbadachusetts Institute of Technology revealed that a single running shoe could include 65 pieces, all of which would normally end up in landfills.
Although shoes can already be recycled, adidas' efforts are different, as they use materials to make entirely new shoes, designed for performance.
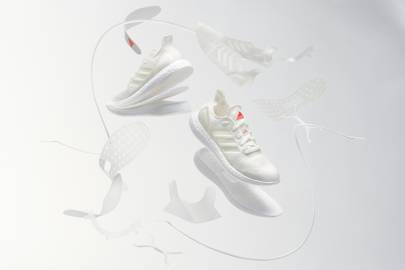
But it is not alone. Nike has a recycling program called Grind. The company recovers old shoes from all manufacturers, throws them into a machine that breaks them down and then uses the materials to make floor coverings. 18 different substances were used to create indoor basketball courts, playgrounds and astroturf football fields.
The minimalist manufacturer of running shoes VivioBarefoot has built shoes from recycled algae and is currently working on a herbal line comprising a field corn material.
In the future, Loop could completely change the way adidas works. Boost material is used throughout the range of lifestyle shoes, not just those designed for runners. There is also potential for a new business model, which could possibly include the option of a shoe subscription. A worn running shoe can be automatically replaced by a recycled model after a certain number of kilometers. This worn pair would then be melted and shipped as a new product.
But it is still in a while. For the moment, adidas must make the loop evolving. Until now, he has only tested a few hundred shoes with his own staff. As he announced the shoes, he also distributed 200 pairs to reporters. These will all be recycled. Those who have been tested internally have all been subjected to standard tests of running shoes, and have been put to the test over more than 500 kilometers of unevenness.
"For the recycling industry, it's peanuts," says Sahanga. "We are talking about one to five tons – it's nothing.These guys deal in the three-digit tons." Williamson adds that "adidas expects the entire recycling and recasting process to take about six months. Indeed, the factory speed technology is not yet in place in its Asian factories. "It aims to work with several materials, several components to create the shoe in a process of badembly that requires a lot of bonding," he said.
The company hopes to offer a limited commercial shoe series by the end of 2020. At this point, it may be the last running shoe you've ever bought.
More beautiful stories from WIRED
– The Play Store is full of nasty and violent games for kids
– Why does the London Tube still not have access to Wi-Fi in tunnels?
– Love, Death & Robots from Netflix, a tedious bad sci-fi
– The sad reality of life under Gangs Matrix in London
– Do you care about online privacy? Then change your phone number
[ad_2]
Source link