[ad_1]



Diagram of the powder bed melting treatment
As part of a recent research project supported by 3DTech, PhD student Dung Ha has been shown to be working on a review of the reuse of PA12 Nylon Powder from the manufacture of 3D printing Multi Jet Fusion (MJF). The author's findings were detailed in the recently published thesis paper titled "A study on the recycling of polyamide 12 powder transformed into 3D printing filaments". If the idea of recycling 3D materials is not quite new, Dung Ha is also exploring how fine powders can be processed. safely and then turned into a filament.
Polyamide nylon 12 (PA12) is chosen by many users because it is both sturdy and flexible, and offers high print performance with strong adhesion of layers. Dung Ha considers that PA12 deserves to be studied and recycled because of its extraordinary properties, but also points out that working with this substance also poses problems, due to the problems of loss of integrity after treatment and of the tendency to absorb water. Since the author is heavily focused on laboratory work, safety is a major priority and an important part of this study; However, the real subject is how the powder can be recycled and reused as a 3D printing filament.
The PA12 is one of the most used 3D printing materials, especially for researchers and engineers. The benefits of this 3D printing powder include:
- Chemical resistance
- Resistance to water
- Strong mechanical properties
- Resistance to stress cracking
- Freestanding for finished products
This powder can be used in various applications, including rapid prototyping, for medical models, etc., and can be improved overall with a variety of different additives such as carbon, glbad or aluminum. 3DTech uses PA12 for its 3D printing products, typically with a particle size of about 55 – 60 μm, and provided the waste used in the study.
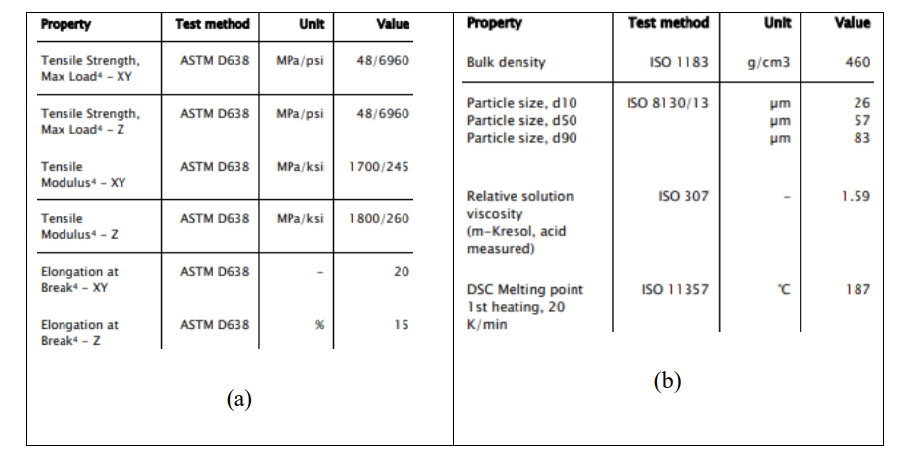
Technical Property (a) and General Property of PA12
The manually collected powder waste consisted of combined powders from various bed printer stations and stored in three sealed plastic boxes and stored in the Arcada laboratory.
![]()
Boxes of powder sealed in the Arcada laboratory.
"As this powder belongs to a group of microparticles and relies on the safety data sheet of the PA12 powder, the explosion of the fine powder and the health effects of the fine powder by inhalation have retained a lot Attention of this thesis, "said Dung Ha.
The most common reason for an explosion of dust clouds is usually a spark forming somewhere in the laboratory. Explosions can occur in some cases, especially if a combination of dust and air is considered dangerous due to intense concentrations. This tends to occur with finer particles.
Safety must be taken into account and, even if flammability is a problem, emissions are also often questioned with regard to 3D printing. Users can easily inhale fine particles posing health risks – and especially because of smaller particles:
"As they can penetrate deep into the lungs; they can offer a chance of chemical absorption into the blood with physical interaction with [the] respiratory system, "says Dung Ha.
Numerous other studies have been conducted in recent years on particulate matter and emissions, such as specific tests of indoor air quality as well as studies of emissions in general. The author addresses here more details than what we usually see, on how users can prevent exposure from affecting or hurting them during an unfortunate explosion. Proper handling procedures should be followed, as well as the wearing of the appropriate protective clothing, such as eyeglbades, lab coats, masks, as well as measures such as washing all areas in contact with the powder, while avoiding eating or drinking in the laboratory.

Virgin (left) and waste (right) powder colors from 3DTech Company.
The chemical degradation and oxidation of unmelted PA12 powder is a problem and, as Dung Ha points out, "the time and heat of [the] The printing bed close to the melting point increases the molecular weight of the PA12 powder, which decreases the viscosity of the PA12 powder. Oxidation also causes yellowing of the brown of the white powder, which requires improvement. To combat degradation and discoloration, other researchers have previously used tungsten carbide (WC) as an additive.

Oxidation in a bucket printed HP MJF
The researcher used a 1.75 mm nozzle, with a constant temperature setting of 180 degrees Celsius, for making filaments from recycled materials. The experiment posed some problems and the adjustment of the WC additive was helpful. However, the researcher concluded that it was simply not possible to make a "high strength 3D product" from a high strength filament. Dung Ha recommends that when developing filaments, users should consider the performance of the 3D FDM printing system used.
Overall, the author concluded that the recycled filaments were successful, resulting in good tensile strength and a good modulus. The filament has also worked successfully in their MakerBot Replicator 2.0, without fouling.
3D printing has opened many doors to many designers and engineers around the world, resulting in an almost global euphoria of creativity. But almost from the beginning of the entertainment, users began to worry about security issues, emissions and what to do with 3D printing waste, including recycling methods, from filament to plastic. Learn more about recycling polyamide 12 filament powder here. What do you think of this news? Let us know your thoughts! Join the discussion on this topic and other topics related to 3D printing on 3DPrintBoard.com.

Filament treatment by Filastruder
[ad_2]
Source link