[ad_1]
Tau was used as an anchor on deepwater projects in Mexico and elsewhere for nearly 20 years, but not on the Norwegian continental shelf as most projects are on shallower waters where the chain is the most sustainable . The use of a fiber rope made from deep-water polymer materials helps to reduce the weight of the anchoring system. A polyester rope is almost weightless in the water and therefore requires smaller dimensions of requirements and winches on the deck. It's also easier to manage. In this way, you save costs and you can anchor in deep water where the solutions with chains become too heavy, "says Mads Arild Eidem, head of materials and subsea operations at DNV GL in Bergen
upgraded a legendary 40-year-old stretching machine with a capacity of 2,900 tons in newer and larger premises.
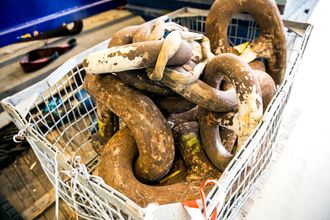
At the submarine technology conference in Bergen, DNV GL organized a demonstration test for operators and equipment suppliers. The test consisted of a polyester cord similar to that now installed at Aasta Hansteen.
After seven minutes – when the tensile strength reached 1909 tons, the two-color polyester rope smoked
The resulting resistance to break was higher than the rope would tolerate according to the supplier's requirements.
Authorities require operators that they document that the rope to be used on the NCS is eligible for the intended use.
Aasta Hansteen is now installed at approx. 1275 meters deep. The floating Spar platform is tied and stabilized with a total tonnage of nearly 4.1 miles.
According to the chief of communications for research and development at Equinor, Eskil Eriksen, Aasta Hansteen has 17 anchor lines where each line is about 2500 meters. These consist of 2400 meters of fiber rope and just over 100 meters of chain up and down. Fibertauet has a diameter of 26 cm and a breaking strength of 1900 tons.
As Long Life
And although the fiber rope is more expensive to produce than the steel chain, it is more flexible and at least as durable at great depth. In other words, they have a lifespan of 20-25 years.
Rope rope is combined with a wealth of fibers welded together on a
We have advanced expertise that allows us to make industrial standards
Gustav Heiberg, Business Development Manager, Materials in DNV GL
Special Way that may vary from one manufacturer to another. The rope tested in Bergen comes from one of the largest suppliers, Lankhorst Euronete Portugal. It is surrounded by a thick outer plastic jacket, made up of a large number of parallel braided delta – with a jacket that connects it together.
– The goal of the cape is to keep the delta together. The rope itself is often laid on the seabed until it is ready for installation depending on the weather window. Ropes sink because there is a little negative weight compared to water, but it takes a lot less resources to install than string because of the weight. Under the casing, we have a sand filter to prevent the penetration of sand and particles, as well as a UV filter so that the polyester is not broken by the sun during installation. The entire rope is traversed by water and is still connected to a lower and upper chain, "says engineer Knut Eide of DNV GL's Anchorage and Sea Lift Technology Center in Bergen [19659018]. 1000 meters and connected together to be longer.
According to Eidem, there is a lot of money to be saved on the use of fiber rope in relation to the chain. In particular, this applies to the great depths of the sea where ordinary steel wire cranes can also be replaced entirely or partly with fiber ropes.
Secret Tests
Qualification tests are usually very secret seasons. No company will give access to material weaknesses – either before use or in connection with maintenance.
– We work the most with mission tests for businesses. We have noticed that the allocations have dropped less after the drop in oil prices, but now it is about to recover. And the other trend is that we receive a lot more customers from other industries, "says Gustav Heiberg, head of business development on test materials in DNV GL.
Besides rope fiber, testing of chains and platforms and ships, but also for fish farming and aquaculture, land and floating wind energy, bridges and railways.
L & # 39; company has testing laboratories at the headquarters of Høvik and Bergen, but only the Bergen machine can take forces up to 2900 tons.There is only one laboratory in the States That can match this strength
– The failure tests have a short time of an hour or two, while the component performance tests can last several weeks.Our experience is that the operators who qualify the materials in the early stages are able to optimize the equipment For example, we received comments that Shell saved $ 100 million to optimize the polyester rope anchoring system.
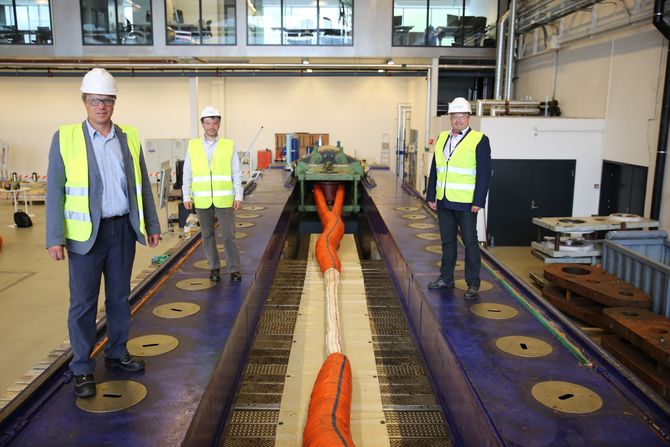
Unique skill
Heiberg thinks there are some. The 40-year stretching machine in Bergen and the test officers represent a unique skill. Recently, DNV GL moved to new larger premises in Bergen.
– In the field of fiber, we work with tensile loads, material analyzes and design analysis checks. We have advanced expertise that allows us to create industry standards, "says Heiberg.
DNV GL also conducts wound analysis at 14 laboratories around the world. In other words, they test for example. how a fiber cable can withstand the stresses of a steel cable if a trawler too approaches an installation anchored by ropes.
Of the more than 1,000 DNV GL damage investigations on installations, 79 were due to anchoring errors with rope or chain.
Currently, this is unusual, but Heiberg also thinks that fiber rope can be equipped with sensors to predict maintenance requirements.
About Resistance: Recently, DNV GL received an Equinor mission to test the enormous 152mm thick chains that anchor the Troll B platform after 20 years of operation. use, which represents an estimated useful life
still as strong and could last for many years. Absolutely unbelievable, Chief Engineer Knut Eide says with enthusiasm.

[ad_2]
Source link