[ad_1]
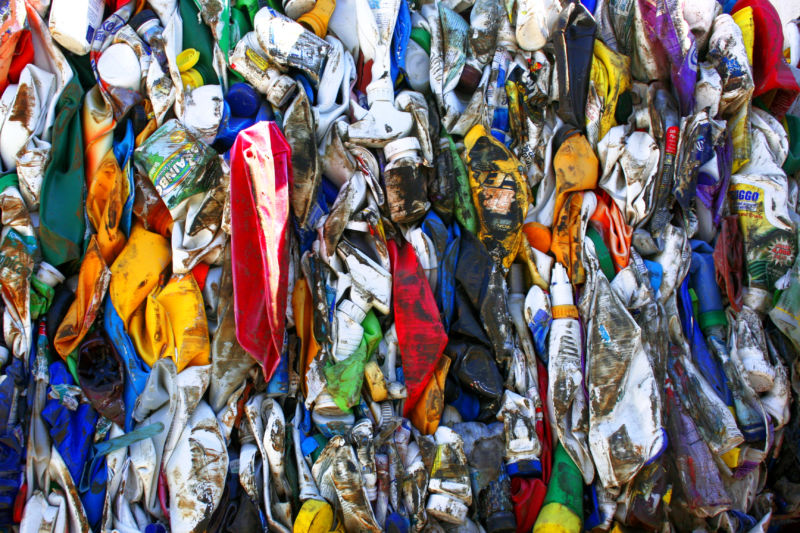
Recycling looks great in principle (because it's the case), but a frustrating number of demons are hiding in the details. For example, while some materials such as aluminum can easily be melted and reconverted into new aluminum cans, recovered plastics tend to be of lower quality than "virgin" materials. This is because recycled plastic retains some of its previous properties, such as Lego bricks that can not be separated. The next plastic you are going to manufacture will not be exactly the same type and the recycled material will not fit perfectly in its new location.
To improve this situation, plastics engineers want to create new materials that can decompose cleanly and easily into the most basic components: individual Lego bricks that can be reassembled to form anything. All pigments, flame retardants and other additives used in plastics increase the difficulty of this task. But a group led by Peter Christensen of Lawrence Berkeley's national laboratory has developed a new plastics processing process that addresses these challenges.
The basic building block of a plastic called a "monomer" – connect the monomers together, and you create "polymers" with the desired physical properties. In this case, the researchers use tricetones and amines as basic monomers. The process of their assembly resembles minor witchcraft (as chemistry often does): the combination of chemical ingredients causes the formation of different building blocks, which then spontaneously assemble.
The real trick is to know how these "diketoamine links" separate. For most plastics, the energy required to separate the blocks is important, making the construction process virtually irreversible. This is why different types of plastics are usually simply melted and used to make something of the same type. But in this case, the bonds between the blocks can be easily broken by a strong acid, producing monomers that are not different from those of the beginning.
The researchers demonstrated the effectiveness of the recycling process with some examples. First, they stained pieces of plastic with different pigments, mixing carbon nanofibers, to boot. After separating the polymer into acid, they were able to extract the monomers easily, leaving behind all the pigments and nanofibers.
In another example, they built a fire-retardant plastic constructed on woven fiberglass, like a tarpaulin. Soaking in strong acid removed the plastic without damaging the fiberglass weave. Another chemical step was to recover a stack of pure monomer powder and another stack of flame retardant additive.
The researchers also tested the physical properties of their "fresh" plastics by reconstituting them with recycled monomers. The results were good, with no change in their function. They also used recycled monomers to make different plastics, confirming that building blocks were ready to be something new.
The fact that these materials are recycled using strong acids rather than high temperatures even opens up the possibility of extracting them from unsorted plastic collections. Traditional plastics are unaffected, so they can be dissolved and collected while traditional plastics remain intact.
This type of progress illustrates the possibilities that could help to "close the loop" on plastics, turning them into materials with an almost infinite usable life rather than a one-time disposable nightmare. One of the ways to improve the economy and the logistics of recycling is simply to make things a lot easier to recycle.
Nature Chemistry, 2019. DOI: 10.1038 / s41557-019-0249-2 (About DOIs).
[ad_2]
Source link