[ad_1]
SpaceX CEO Elon Musk believes the company may eventually be able to build the gigantic Starship spacecraft and Super Heavy launcher (formerly BFR). less than Falcon 9 / Falcon Heavy, a rocket 3 to 9 times smaller than the BFR.
While it's certainly one of the craziest and craziest priorities the CEO has set out over the years, there may be many ways – even with good skills – that Starship's production costs Super Heavy could finally compare favorably to SpaceX Vehicles' Falcon launch family. Nevertheless, there are at least as many ways in which a new generation rocket can (or should) never be able to beat the cost of producing what is actually a much simpler rocket.
It will seem unlikely, but I think it is possible to build Starship / Super Heavy at a lower price than Falcon 9.
– Elon Musk (@elonmusk) February 11, 2019
Dirty boosters makes dirt cheap
On one side, Musk might not necessarily be wrong, especially if we throw several bones at the CEO in the interpretation of his brief tweet. BFR, in its simplest form, will require 38 rocket engines to meet its nominal performance targets, 7 on Starship and 31 on Super Heavy. As a considerably more advanced, larger and much more complex engine, Raptor will cost (with little doubt) much more per engine than the relatively simple Merlin 1D. BFR avionics (on-board computers, electronics, wiring, beams) is probably a more known quantity, which means that the costs will likely be comparable to or even lower than those of Falcon 9 when measured in proportion to the total cost of the aircraft. vehicle. Assuming that BFR can use exactly the same cold gas thrusters currently driving the Falcon 9, this cost should only increase proportionally to the size of the vehicle. Finally, Starship will not require a deployable payload fairing (approximately 10% of the Falcon 9 production cost).
All this means that Starship / Super Heavy will probably start with a much higher cost-effectiveness ratio than Falcon 9, thanks to almost ten years of experience in the construction, flight and renovation of the rocket since its debut in 2010 Nevertheless, BFR will need to take into account entirely new structures, such as six large tripod flaps / wings and their actuators, entirely new thrust structures (Falcon 9-related) for both stages, and more. If we consider Starship in itself, the production of a human-capable spacecraft that can safely house dozens of people in space for weeks or months will almost certainly compete with the cost of production of airliners, where a 737 – with nearly half a century of production and heritage of theft – still holds a price tag of 100-130 million dollars.
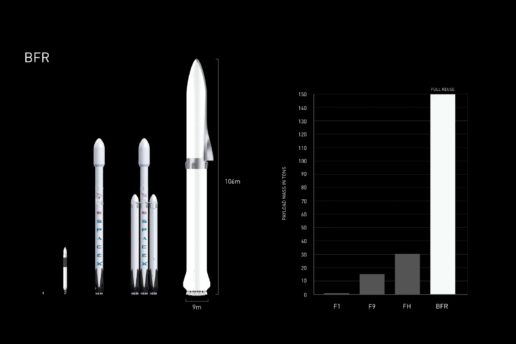
BFR shown on the scale with Falcon 1, 9 and Heavy. (SpaceX)
Even at full throttle, even the top floor of the BFR spacecraft will be nearly twice as powerful as a Falcon 9 booster. This power could easily destroy a fixed concrete slab and even the rocket if it were not hit. (SpaceX)
"data-medium-file =" https://www.teslarati.com/wp-content/uploads/2018/09/BFR-2018-Moon-burn-detail-SpaceX-300×151.jpg "data-large-file = "https://www.teslarati.com/wp-content/uploads/2018/09/BFR-2018-Moon-burn-detail-SpaceX-10-10×515.jpg" src = "https: //www.teslarati. com / wp-content / uploads / 2018/09 / BFR-2018-detail-space-engraving-spaceX-516×260.jpg "width =" 516 "height =" 260 "align =" left "title =" BFR 2018 detail of engraving on the moon (SpaceX) "/>
SpaceX updated Starship's design with seven Raptor variants at sea level, simplifying development. (SpaceX)
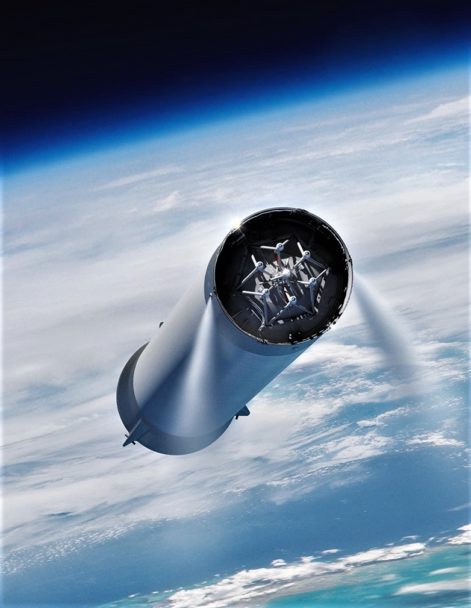
BFR Booster, now known as Super Heavy. (SpaceX)
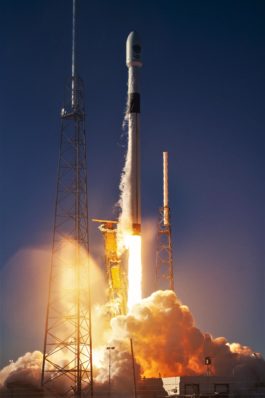
Falcon 9 B1054 – without ailerons and landing legs – took off for the first and last time in support of the first launch of the GPS III satellite by the USAF. (SpaceX)
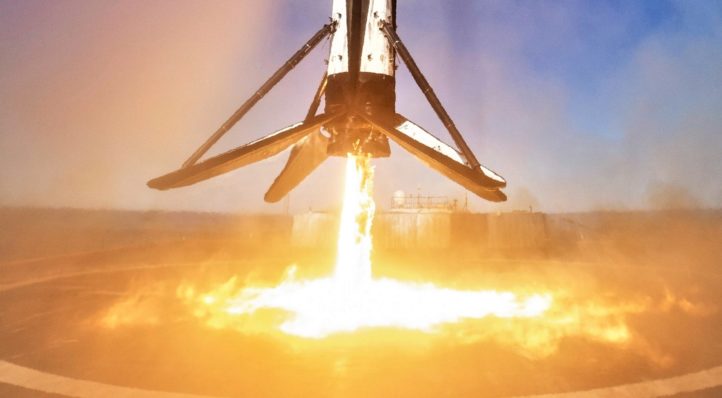
The Falcon 9 B1046 is photographed here after its successful third launch, December 2018. (SpaceX)
By adding an additional assumption, the most forgiving interpretation of Musk's tweet assumes that he actually submits only the overall structure (without engines and no material material to the crew) of BFR in relation to to Falcon 9. In other words, a stainless steel of about 300 tons could steel rocket structure (BFR) cost the same amount or less to manufacture as an aluminum-lithium alloy rocket structure. about 30 tons (Falcon 9 / Heavy)? Musk estimated that the cost of stainless steel alloys (Series 300) for use in BFRs was approximately $ 3 per pound ($ 6.60 / kg), while aluminum-lithium alloys used in aerospace (and 9) are sold for approximately $ 20 / lb ($ 44 / kg) *. Thus, purchasing the materials needed to build the basic structures of BFR and Falcon 9 would cost about $ 7.5 million and $ 5 million, respectively.
Assuming that the process of assembling, welding and integrating Starship and Super Heavy structures is 5 to 10 times cheaper, simpler and less labor intensive, there is no reason why. It is in fact not inconceivable that the cost of building the BFR structure could compete with Falcon 9 after production has stabilized after the prototyping phase of the new rocket and the end of the manufacturing processes.
*Very rough estimate, difficult to find a public cost per unit mass among modern Al-Li suppliers

Costs vs. benefits
In contrast, stainless steel rockets have never been more profitable than vehicles using alternative materials. The only orbital class launchers to use stainless steel tanks (and balloons) are the Atlas Propeller and the Centaur's top tier, the Atlas dating back to the late '50s and its launch in the early' 60s. Atlas launches in stainless steel ended in 2005 with the latest Atlas III mission, while many Centaur forms continue to fly regularly on ULA's Atlas V and Delta IV satellites.
On the basis of a 1966 contract between NASA and General Dynamics, shortly after the completion of much of Centaur's tortured construction, Centaur's upper floors cost about $ 25 million each ($ 2018). In 1980, equipment needed to launch a 1500 kg Comstar I satellite dedicated to Atlas-Centaur cost about $ 201 million in the United States in 2018 ($ 71 million ($ 71 million, including administrative costs) ): $ 22.4 million for Centaur and $ 17.6. M for Atlas. For Atlas, the rocket cell (tanks and general structure) was purchased for about $ 8.5 million. This version of Atlas-Centaur (Atlas-SLV3D Centaur-D1A) could lift approximately 5,100 kg in low Earth orbit and 1,800 kg in geostationary transfer orbit, while it measured approximately 40 m (130 ft) in height, had a tank diameter of 3.05 m (10 ft) and weighed approximately 150 t (330,000 lb) fully filled with fuel.
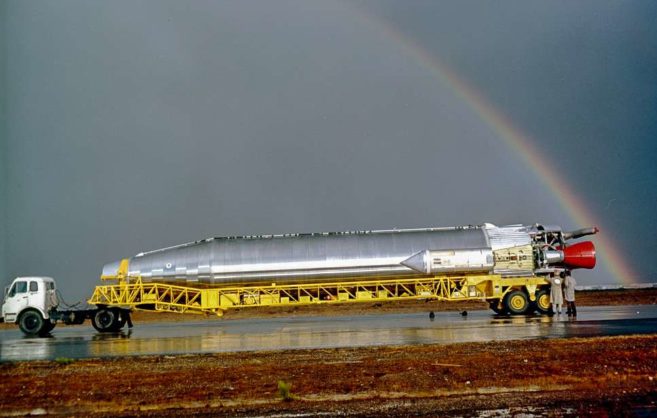
Atlas shows its shiny steel ball tanks. (SDASM)
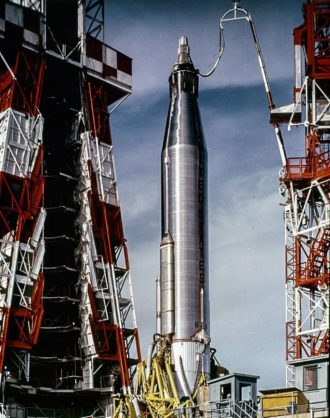
The original space atlas, known as SM-65, is shown here with a Mercury space capsule. (NASA)
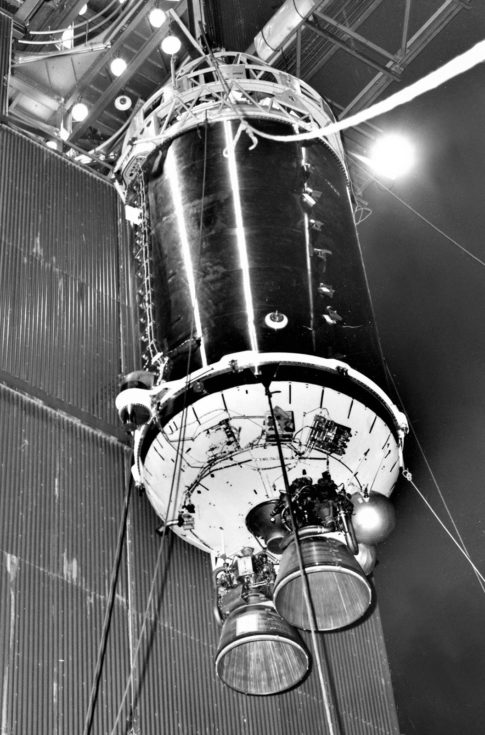
An upper floor of Centaurus is shown here in 1964. (NASA)
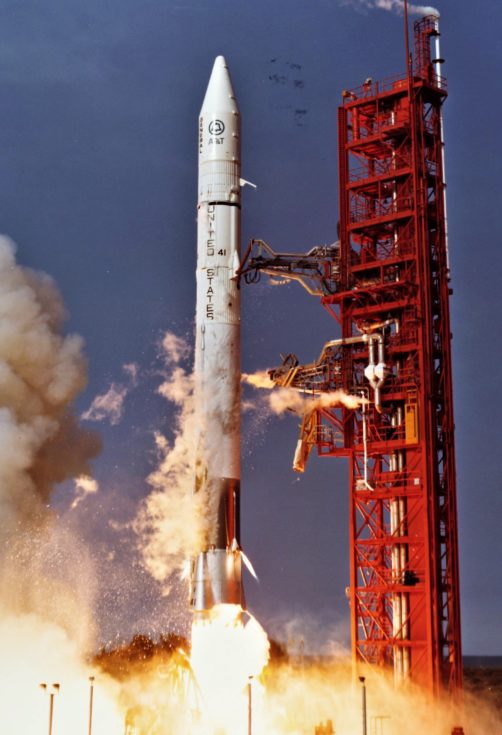
Atlas SLV3D is photographed here in the process of launching a Comstar I satellite.
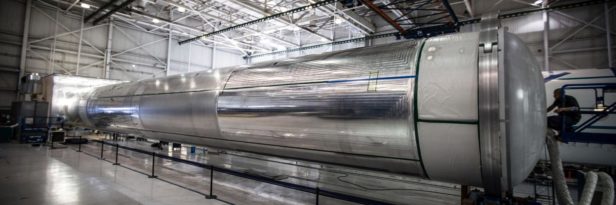
A reminder of Falcon 9 is seen here near the end of the weld of his tank, just before painting. (SpaceX)
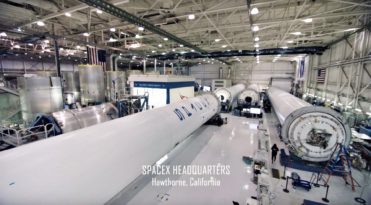
An overview of the SpaceX plant in Hawthorne in early 2018. (SpaceX)
Very loosely, this stainless steel Atlas variant was about twice as large and twice as capable as the first version of Falcon 9 adapted to the flight, at about the same launch price ($ 60 to $ 70 million). What does this storybook tell us about the prospects of a Starship and a Super Heavy stainless steel? Not a lot. It is very simple to try to understand and separate the official claims relating to SpaceX's next-generation launch architecture: a single family of rockets in the history of the industry ( Atlas) regularly flew with stainless steel propellant tanks, a line of a half century that completed its final launch in 2005.
In general, an industrial sample of plus or minus a sample does not make it easy to draw specific conclusions about a given technology or practice, and SpaceX – according to CEO Elon Musk – intends to fully exceed advanced technologies Rocket Tank in stainless steel with BFR. In the end, the American Marietta / Martin Marietta / Lockheed Martin has never been able to produce variants of the Atlas family of stainless steel at a more competitive cost than that of Falcon 9, despite the use by the latest rocket of a much more expensive metal alloy throughout its main business. tanks and structure.
At least 10X cheaper
– Elon Musk (@elonmusk) February 11, 2019
At one point, it is even interesting to wonder whether the unit cost of Starship and Super Heavy should have an impact on their design and construction, at least within reasonable limits. If the goal of BFR is to significantly reduce the launch cost by drastically improving the ease of reuse, it would be really weird (and totally unintuitive) to be able to achieve these goals without greatly increasing the cost of buying initial hardware. Perhaps the closest comparison to BFR's goals, modern airliners are expensive (between $ 100 million and $ 500 million each) because of extraordinary reliability, performance, efficiency and longevity. that customers and regulators demand from them, although these costs are certainly not absolute. the lowest, they could be in a perfect manufacturing scenario.
At the end of the day, it seems that Musk is more and more convinced that the pivot to stainless steel could ultimately produce the BFR simultaneously. "Better, faster, [&] cheaper". As unlikely as it may be, Starship and Super Heavy could, if this were to be the case, be an unfathomable advance for reliable and affordable access to space. It could also be another case of Musk's excitement and optimism that overcame him and exaggerated a given product well beyond what he was finally able to achieve. Time will tell us!
Check out Teslarati newsletters for quick updates, on-the-ground perspectives and unique insights into SpaceX rocket launch and recovery processes!
[ad_2]
Source link