[ad_1]
Elon Musk, CEO of SpaceX, said the first complete engine of the spacecraft to test had already been damaged less than three weeks after the start of the campaign, paving the way for the upcoming resumption of the second complete Raptor. future.
According to Musk, although most of the damaged components of the Raptor pathfinder must still be easily reusable, the assembly of the second finalized engine is "nearing completion" and Raptor will support short-term testing rather than waiting for repairs to the first one. engine. This is undoubtedly an extraordinarily aggressive test program, especially for a state-of-the-art, state-of-the-art rocket propulsion system, but these developments are far more encouraging than they are. ultimately.
Merlin. The maximum pressure of the chamber damaged the Raptor SN 1 (as expected). Most parts can be reused, but the next tests will be on SN 2, which is almost complete.
– Elon Musk (@elonmusk) February 21, 2019
Although the Raptor engine family has started its static fires since September 2016, the SpaceX propulsion team has finalized the basic design of Raptor and has completed assembly, shipping and handling. Integrated static shooting of the first complete engine on February 3, considerably less than three weeks. before Musk took to Twitter. In addition to confirming that the new Raptor had been damaged in its last static fire several days earlier, Musk said the failure (unsurprisingly) was mainly attributed to the engine having reached the highest pressures in the chamber.
The main Raptor combustion chamber (the drill directly above the nozzle) was designed to operate at nominal pressures of over 250 bar (3600+ psi) and reliably withstand these performances. in the Raptor combustion chamber. Musk in a tweet from 2018 is an example of choice: its pre-oxygen burner, used to convert the liquid propellant into a high-speed gas that can then feed a dedicated oxygen turbopump. In addition to the extremely corrosive environment created by extremely hot oxygen gas, the pre-burner must also withstand pressures of up to 800 bar or 12,000 psi.
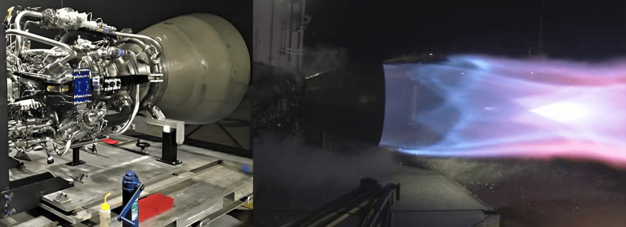
SpaceX's world-class rocket propulsion team progressed during the first large-scale Raptor trials at an incredible speed. (SpaceX)
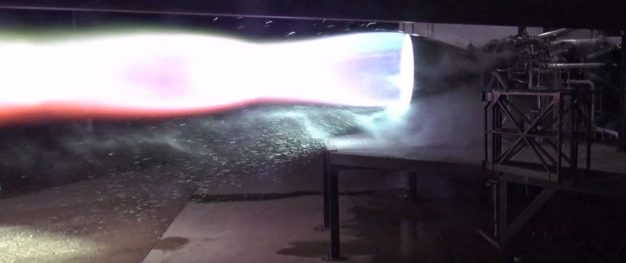
First large-scale Raptor static firing attempt on February 3rd. (SpaceX)
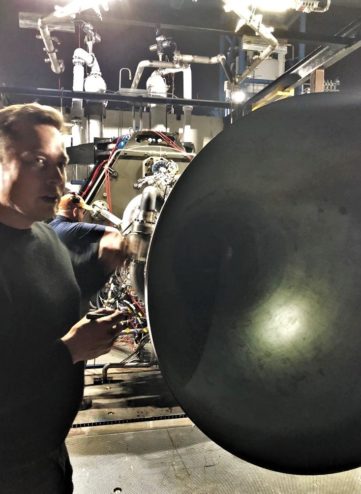
Raptor's business ends with a musk-scale. (Elon Musk)
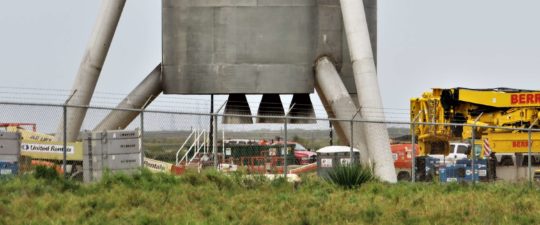
Starship revealed three Raptor models when SpaceX technicians moved the support assembly to the ground. (NSF – bocachicagal)
Even at full throttle, even the top floor of the BFR spacecraft will be nearly twice as powerful as a Falcon 9 booster. This power could easily destroy a fixed concrete slab and even the rocket if it were not hit. (SpaceX)
"data-medium-file =" https://www.teslarati.com/wp-content/uploads/2018/09/BFR-2018-Moon-burn-detail-SpaceX-300×151.jpg "data-large-file = "https://www.teslarati.com/wp-content/uploads/2018/09/BFR-2018-Moon-burn-detail-SpaceX-10-10×515.jpg" src = "https: //www.teslarati. com / wp-content / uploads / 2018/09 / BFR-2018-detail-space-engraving-spaceX-447×225.jpg "width =" 447 "height =" 225 "align =" left "title =" BFR 2018 detail of engraving on the moon (SpaceX) "/>
SpaceX updated Starship's design with seven Raptor variants at sea level, simplifying development. (SpaceX)
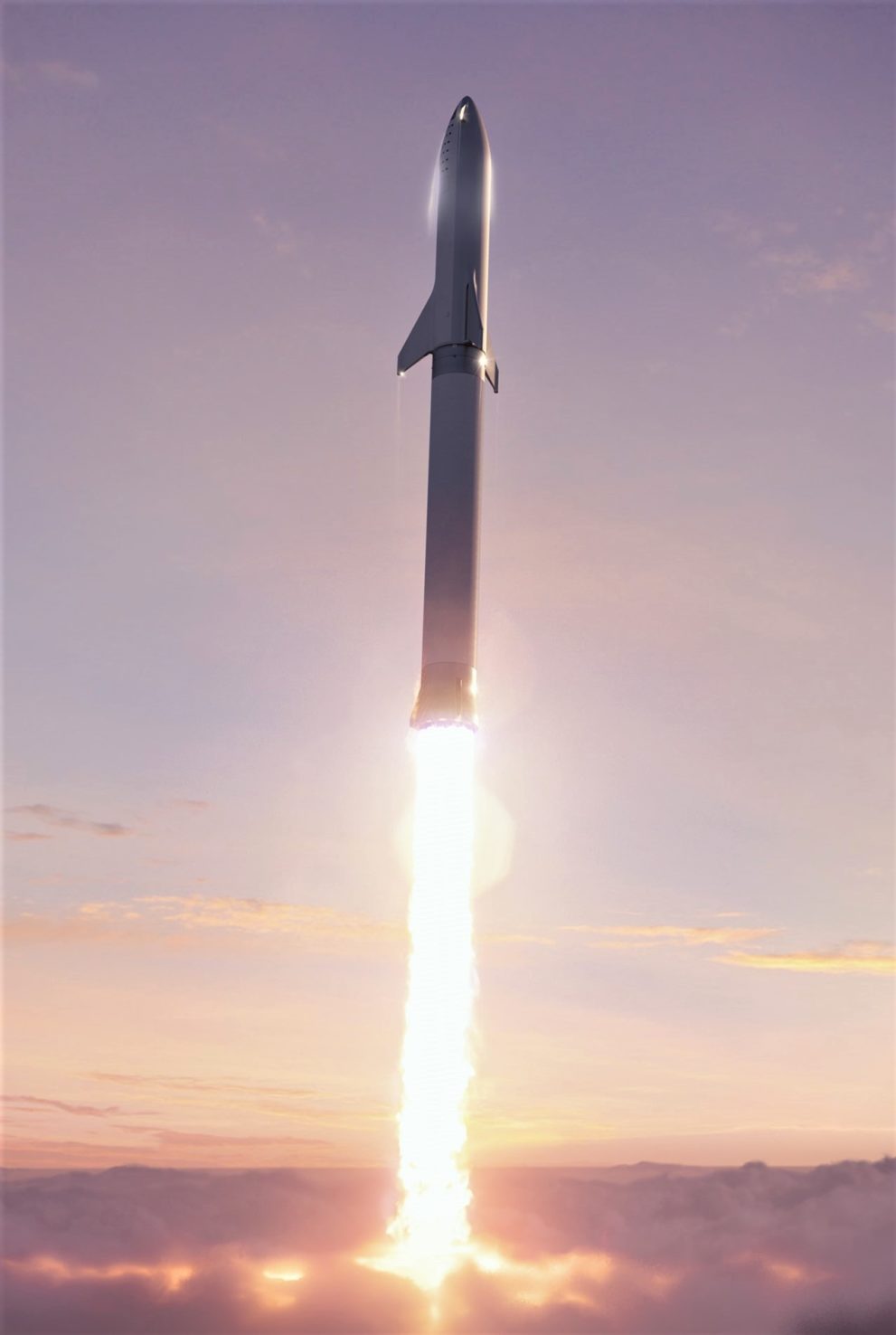
BFR (2018) goes through a cloud layer shortly after its launch. (SpaceX)
A lack of technical detail means that it's hard to know what thrust or pressure the Musk master bedroom had in mind when talking about exotic alloys that would be needed to survive these pressures, but the performance stats of A Raptor with a pre-burner operating at over 800 bar would probably be superior to anything that Musk has described so far. In other words, it is reasonable to assume that Raptor has not yet been pushed to achieve these performance levels, although this remains a distant possibility. It is more likely that more than 800 bars in the pre-burner oxygen is an extreme goal that will require concerted research, development and optimization, with Raptor suffering damage below these levels while reaching staggering numbers.
– Elon Musk (@elonmusk) February 4, 2019
For an engine as complex as Raptor, there are countless dozens of potential failure modes whose onset would hardly be surprising for an engine just days after large scale testing. First and foremost, the Raptor test program organized by SpaceX's world-class propulsion team – whether autonomous or motivated by reckless spreadsheet management – was extremely fast, taking the first high-performance Raptor ever built from immobilization to more than 90% of the thrust pressure and the chamber pressure of almost 270 bar (less than a week). During the same period, more than half a dozen static fire tests (ranging from 1 to 10 seconds) were performed.
A few days after February 10, when Raptor reached a pressure comparable to that of the most modern engines (notably the RD-180/190/191), the engine was apparently pushed even higher, reaching a pressure in the chamber ( and therefore thrust) that has caused damage to some of the most sensitive parts of the engine's piping. Despite the fact that Raptor's second production is apparently already "almost complete," Musk suggested that modifications (of unknown severity) would already be introduced to mitigate the failure modes faced by Raptor SN01.
SN2 has changes that should help
– Elon Musk (@elonmusk) February 21, 2019
In a sector where NASA and subcontractors like Aerojet-Rocketdyne will spend months performing static fire tests of space shuttle engines, which have literally performed dozens (if not more) of missions in orbit and whose performance and reliability have been measured in Hundreds of thousands of seconds, the speed and agility of SpaceX's Raptor development program and tests are breathtaking. What remains to be seen is how the end results (ie operational Raptor) will be of comparable reliability and success, but an attitude that actively accepts and even pursues destructive testing can ultimately only benefit the finished product at the expense of the destroyed material. and many lessons on the ground have learned the hard ways.
Given the immense success of SpaceX's Merlin engine line-up and the development and continuous improvement strategy that brought it from Merlin 1A to 1D and MVacD, SpaceX clearly does not have to fumble in the field of Raptor's research and development.
Check out Teslarati newsletters for quick updates, on-the-ground perspectives and unique insights into SpaceX rocket launch and recovery processes!
[ad_2]
Source link