[ad_1]
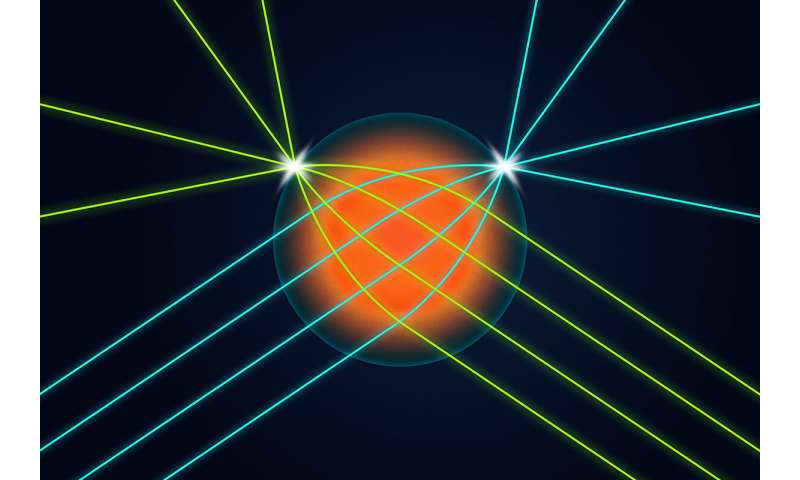
Researchers in Illinois have developed a spherical lens that allows light entering the lens from any direction to be focused into a very small point on the lens surface exactly opposite to the direction of ‘Entrance. This is the first time that such a lens has been designed for visible light. Credit: Graphic by Michael Vincent
Researchers have developed new 3-D printed microlenses with adjustable refractive indices – a property that gives them highly specialized light focusing abilities. This breakthrough is poised to improve imaging, computing and communications by dramatically increasing the data routing capacity of computer chips and other optical systems, the researchers said.
The study was conducted by Paul Braun and Lynford Goddard, researchers at the University of Illinois at Urbana-Champaign, and is the first to demonstrate the ability to adjust the direction in which light bends and travels to through a lens with an accuracy of less than a micrometer.
The results of the study are published in the journal Light: science and application.
“Having the ability to fabricate optics with different optical shapes and parameters offers a solution to common problems encountered in optics,” said Braun, who is a professor of materials science and engineering. “For example, in imaging applications, focusing on a specific object often results in blurred edges. Or, in data transfer applications, higher speeds are desired without sacrificing space on a computer chip. new lens manufacturing technique solves these problems in one. integrated camera. “
As a demonstration, the team made three lenses: a flat lens; the world’s first visible-light Luneburg lens – a previously impossible to manufacture spherical lens with unique focusing properties; and 3D waveguides which can enable massive data routing capabilities.
“A standard lens has a single index of refraction and therefore only one path that light can travel through the lens,” said Goddard, who is a professor of electrical and computer engineering. “By controlling the internal refractive index and the shape of the lens during manufacturing, we have two independent ways of bending light inside a single lens.”
In the lab, the team uses a process called direct laser writing to create the lenses. A laser solidifies liquid polymers and forms small geometric optical structures up to 100 times smaller than a human hair. Direct laser writing has been used in the past to create other microlenses that only had a single index of refraction, the researchers said.
“We addressed the limitations of refractive index when printing inside a nanoporous scaffold support material,” Braun said. “The scaffold locks the printed micro-optics in place, allowing the fabrication of a 3D system with suspended components.”
Researchers theorize that this control of the refractive index is the result of the polymer setting process. “The amount of polymer that gets trapped in the pores is controlled by the intensity of the laser and the exposure conditions,” Braun said. “Although the optical properties of the polymer itself do not change, the overall refractive index of the material is controlled depending on the laser exposure.”
Team members said they expected their method to have a significant impact on the fabrication of complex optical components and imaging systems and to be useful in advancing personal computing.
“A good example of the application of this development will be its impact on transferring data to a personal computer,” said Goddard. “Today’s computers use electrical connections to transmit data. However, data can be sent at a significantly higher rate using an optical waveguide, as different colors of light can be used to send signals. data in parallel. A major challenge is that conventional waveguides can only be fabricated in a single plane and so a limited number of points on the chip can be connected. By creating three-dimensional waveguides we can dramatically improve data routing, transfer speed and power efficiency. ”
3-D printed glass improves flexibility of optical design
Christian R. Ocier et al. Light: science and applications (2020). DOI: 10.1038 / s41377-020-00431-3
Provided by the University of Illinois at Urbana-Champaign
Quote: Researchers Facing Optics and Data Transfer Challenges with 3D Printed Lenses (December 3, 2020) Retrieved December 4, 2020 from https://phys.org/news/2020-12-optics-data -transfer-3d-printed-lens .html
This document is subject to copyright. Other than fair use for private study or research purposes, no part may be reproduced without written permission. The content is provided for information only.
[ad_2]
Source link