[ad_1]
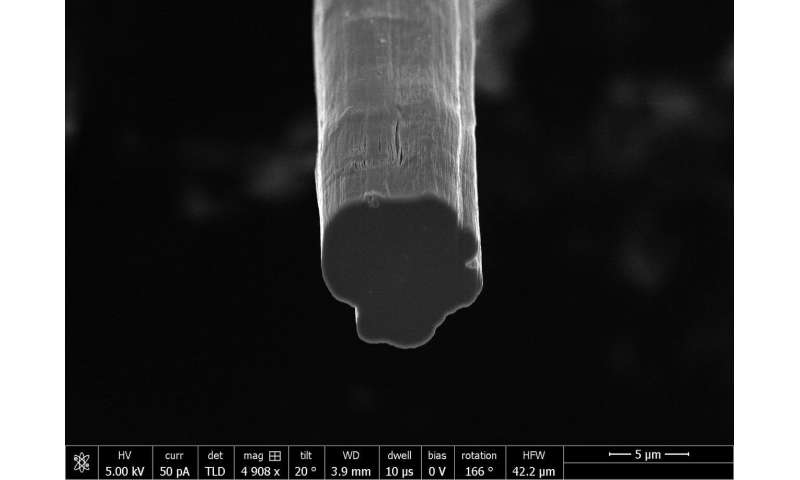
The cross section of a fiber produced at Rice University contains tens of millions of carbon nanotubes. The lab is continually improving its method of making fibers, which tests now show are stronger than Kevlar. Credit: Pasquali Research Group
Carbon nanotube fibers made at Rice University are now stronger than Kevlar and gradually increase the conductivity of copper.
The rice laboratory of chemical and biomolecular engineer Matteo Pasquali reported in Carbon it has developed its strongest and most conductive fibers to date, made of long carbon nanotubes through a wet spinning process.
In the new study by Rice graduate students Lauren Taylor and Oliver Dewey, researchers noted that wet-spun carbon nanotube fibers, which could lead to breakthroughs in a multitude of medical applications and materials, have doubled in strength and conductivity every three years, a trend that spans nearly two decades.
While it may never emulate Moore’s Law, which has set a benchmark for advancements in computer chips for decades, Pasquali and his team are doing their part to advance the method they pioneered to make nanotube fibers. of carbon.
The lab’s filiform fibers, with tens of millions of nanotubes in cross section, are being studied for use as bridges to repair damaged hearts, as electrical interfaces to the brain, for use in cochlear implants, as flexible antennae, and for automotive and aerospace applications.
They are also part of the Carbon Hub, a multi-university research initiative launched in 2019 by Rice with support from Shell, Prysmian and Mitsubishi to create an emissions-free future.
“Carbon nanotube fibers have long been touted for their potentially superior properties,” Pasquali said. “Two decades of research at Rice and elsewhere have made this potential a reality. Now we need a global effort to increase production efficiency so that these materials can be made with zero carbon dioxide emissions and potentially with the simultaneous production of clean hydrogen. “
“The purpose of this article is to highlight the record properties of fibers produced in our lab,” Taylor said. “These improvements mean that we now outperform Kevlar in strength, which for us is a huge achievement. With just another doubling, we would outperform the strongest fibers on the market.”
Flexible rice fibers have a tensile strength of 4.2 gigapascals (GPa), compared to 3.6 GPa for Kevlar fibers. Fibers require long nanotubes with high crystallinity; that is, regular networks of rings of carbon atoms with few defects. The acidic solution used in the rice process also helps reduce impurities that can interfere with fiber strength and improves the metallic properties of nanotubes through residual doping, Dewey said.
“The length, or aspect ratio, of nanotubes is the defining characteristic that determines the properties of our fibers,” he said, noting that the area of the 12 micron nanotubes used in rice fiber facilitates better van der Waals connections. “It also helps the collaborators who grow our nanotubes optimize solution processing by controlling the number of metal impurities in the catalyst and what we call amorphous carbon impurities.”
The researchers said that the conductivity of the fibers improved to 10.9 megasiemens (millions of siemens) per meter. “This is the first time that a carbon nanotube fiber has crossed the 10 mega-step threshold, so we have reached a new order of magnitude for nanotube fibers,” Dewey said. Normalized for weight, he said that rice fibers reach about 80% of the conductivity of copper.
“But we are outperforming platinum wire, which is a great achievement for us,” Taylor said, “and the thermal conductivity of the fiber is better than any metal and any synthetic fiber, at the except pitch graphite fibers. “
The lab’s goal is to make the production of high-quality fiber efficient and inexpensive enough to be incorporated by industry on a large scale, said Dewey. Solution processing is common in the production of other types of fibers, including Kevlar, so factories could use familiar processes without major retooling.
“The advantage of our method is that it is essentially plug and play,” he said. “It is inherently scalable and fits into the way synthetic fibers are already made.”
“There is an idea that carbon nanotubes will never be able to achieve all of the properties that people have loved for decades,” Taylor said. “But we are making good gains year after year. It is not easy, but we still believe that this technology will change the world.”
Co-authors of the article are Rice’s alumnus Robert Headrick; graduate students Natsumi Komatsu and Nicolas Marquez Peraca; Geoff Wehmeyer, assistant professor of mechanical engineering; and Junichiro Kono, Karl F. Hasselmann Professor of Engineering and Professor of Electrical and Computer Engineering, Physics and Astronomy, Materials Science, and Nanotechnology. Pasquali is AJ Hartsook Professor of Chemical and Biomolecular Engineering, Chemistry and Materials Science, and Nanoengineering.
Researchers advance characterization and purification of nanotube wires and films
Lauren W. Taylor et al. Improved properties, increased production and a path to wide adoption of carbon nanotube fibers, Carbon (2020). DOI: 10.1016 / j.carbon.2020.07.058
Provided by Rice University
Quote: Team advocates for high performance carbon nanotube fibers for industry (August 17, 2020) retrieved August 18, 2020 from https://phys.org/news/2020-08-team-case-high-performance- carbon-nanotube. html
This document is subject to copyright. Other than fair use for private study or research purposes, no part may be reproduced without written permission. The content is provided for information only.
[ad_2]
Source link